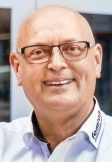
P
roduktions- und Montage-Prozesse nach modernsten Methoden stehen im Fokus der Femron AG in Feuerthalen. Nach ihrem Start im Jahre 2009 hatte die Firma mit Lieferschwierigkeiten zu kämpfen, bis sie sich entschloss, das One- Piece-Flow-Prinzip einzuführen, das sich von dem Lean-Production-System ableitet. Femron Geschäftsführer Norbert Schorpp sagt: „Natürlich erfordert das Investitionen, denn eine einfache Werkbank ist billiger als ein One-Piece- Flow-Arbeitsplatz. Diese Investition rechnet sich jedoch bereits innerhalb eines Jahres… Es bringt sehr viel an Effizienz: wir haben die Montage- und Durchlaufzeiten aller unserer Produkte glatt halbiert.“Mit Hilfe von Präzisionsmechanik stellt Femron komplexe Apparate und mechanische Bauteile für die Medizinaltechnik, Pharma- und Optikindustrie her. Die in diesen Sparten verwendeten Geräte zeichnen sich durch eine hohe Präzision und eine überaus geringe Toleranz für Abweichungen aus. Das erfordert bei der Herstellung eine aussergewöhnlich exakte Arbeitsweise und eine Qualität, die sich nur mit detaillierter Planung und hoher Prozesssicherheit erreichen lässt. Femron produziert u. a. Geräte der Firma MBV, wie etwa den MAS-100 NT zur mikrobiologischen Luftüberwachung in Reinräumen und hygienisch überwachten Bereichen, mit automatischem Kalibrier-Zyklus. Das Unternehmen beschäftigt 25 Mitarbeiter.
Lean Production, One-Piece-Flow und Kanban
Thema des Anlasses in Feuerthalen war „One- Piece-Flow und Kanban“ (Abb. 1). Grundlage für die nach diesem Prinzip angewandte Fertigungstechnik ist Lean Management. Was heisst Lean Production in Unternehmen in der Praxis und welche Methoden und Werkzeuge werden eingesetzt, welche Chancen bieten sich?
An praktischen Beispielen konnten die Teilnehmer die Produktions- und Montage-Prozesse nach modernsten Methoden miterleben. Sie erhielten an diesem Event viele interessante Eindrücke zur Entwicklung, Produktion und den Vertrieb in einem internationalen Unternehmen.
An praktischen Beispielen konnten die Teilnehmer die Produktions- und Montage-Prozesse nach modernsten Methoden miterleben. Sie erhielten an diesem Event viele interessante Eindrücke zur Entwicklung, Produktion und den Vertrieb in einem internationalen Unternehmen.
Lean Production
Lean Production bietet neue Lösungsansätze zur Effizienzsteigerung und zur Vermeidung von Verschwendung. Durch Anwendung dieses Prinzips entstehen Produktionskonzepte mit durchgängig integrierten Prozessen (inkl. Einbindung in das ERP) und einem sehr hohen Rationalisierungseffekt. Lean als Führungs- und Organisationskonzept fordert alle Mitarbeiter – von der Fertigung bis zum Management – im Betrieb heraus.
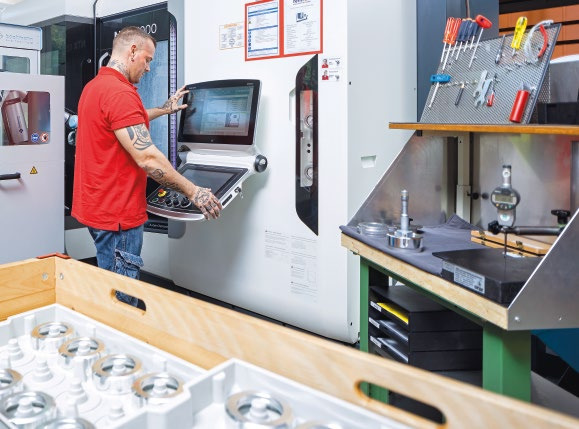
One-Piece-Flow
Das One-Piece-Flow-Prinzip stammt ursprünglich aus de 85468239 m Toyota-Produktionssystem. Es wird auch als mitarbeitergebundener Arbeitsfluss bezeichnet und wird meist in Lean Production- Umgebungen angewendet. Als solches fördert es die Flexibilität und Veränderung im Unternehmen und dient einer optimierten Gestaltung sowohl der einzelnen Arbeitsplätze als auch der administrativen Wertschöpfungskette. Durch One-Piece-Flow in der Montage erhält man direkt Rückmeldungen zur Qualität der Produkte, so dass die Qualität aller Standards jederzeit gewährleitet ist. One-Piece-Flow-Umgebungen sind nach diesem Prinzip logistisch durchorganisierte Fliessfertigungen, bei denen die Mitarbeiter das Werkstück durch die verschiedenen Bearbeitungsgänge bis zu seiner Fertigstellung begleiten.
Kanban
Unter Kanban versteht man eine Methode der Produktions- Prozesssteuerung. Das Vorgehen orientiert sich ausschliesslich am tatsächlichen Verbrauch von Materialien am Bereitstellungs- und Verwendungsort und verhindert Ressourcenverschwendung. Das Ziel von Kanban ist die Optimierung der Kostenund Qualitätsstatus eines Unternehmens durch eine Reduktion der lokalen Bestände von Vorprodukten, die in den Produkten der nächsten Stufe verbaut werden, eine Reduzierung der Fertigungskosten und der Fertigungs- und Montagefehler.
Pharmazeutische Anlagen und Fertigungsprozesse unterliegen strengen Validierungskriterien, um eine reproduzierbare Qualität zu gewährleisten. Das gilt auch für die Herstellung der Geräte und Bauteile, die später in der Pharmaproduktion und Medizintechnik zum Einsatz kommen. Besondere Ansprüche werden an die verwendeten Rohmaterialien wie Kunststoffe, Aluminium und rostfreier Edelstahl gestellt. Auch während der Bearbeitung und Reinigung müssen Faktoren wie Sterilität und Biokompatibilität berücksichtigt und überwacht werden. Durch das One-Piece-One-Flow-Prinzip in der Montage erhält man außerdem direkt Rückmeldungen zur Qualität der Produkte, so dass die Einhaltung aller Standards jederzeit gewährleistet werden kann.
Pharmazeutische Anlagen und Fertigungsprozesse unterliegen strengen Validierungskriterien, um eine reproduzierbare Qualität zu gewährleisten. Das gilt auch für die Herstellung der Geräte und Bauteile, die später in der Pharmaproduktion und Medizintechnik zum Einsatz kommen. Besondere Ansprüche werden an die verwendeten Rohmaterialien wie Kunststoffe, Aluminium und rostfreier Edelstahl gestellt. Auch während der Bearbeitung und Reinigung müssen Faktoren wie Sterilität und Biokompatibilität berücksichtigt und überwacht werden. Durch das One-Piece-One-Flow-Prinzip in der Montage erhält man außerdem direkt Rückmeldungen zur Qualität der Produkte, so dass die Einhaltung aller Standards jederzeit gewährleistet werden kann.
Eine Erfolgsgeschichte
Wie schafft es Femron, international konkurrenzfähig zu bleiben und kosteneffizient am Werkplatz Schweiz zu produzieren?
Die Produktion bei Femron basiert auf Lean Production und gleichermassen auf den vielschichtigen Leistungen durch sorgfältig ausgebildete Mitarbeiter, auf dem schonenden Umgang mit Ressourcen sowie auf intelligenter Automation und schlanker Prozesse entlang der gesamten Wertschöpfungskette – von der Idee bis zum fertigen Produkt mit allen dazugehörenden Services. Durch die mit dem Lean Prinzip einhergehende massive Senkung der Gesamtkosten bei intelligentem Umgang mit einer erhöhten Variantenvielfalt – z.B. der Luftkeimsammler – ist es Femron gelungen, sich erfolgreich am Markt zu positionieren und wettbewerbsfähig zu bleiben. Mithilfe von Lean Management wurden Konzepte entwickelt, mit deren Hilfe die Herstellkosten für das Kernprodukt der Firma signifikant gesenkt werden konnten. Massgeblich für den Erfolg war die Einführung eines Flussprinzips, das eine kontinuierliche Versorgung von Fertigungslinien sicherstellt, die Durchlaufzeit reduziert und die Implementierung des Kundentakts als Schrittmacher, der den Rhythmus der Produktion vorgibt. Die diversen Verschwendungsarten in der Produktion wurden abgestellt.
Die Produktion bei Femron basiert auf Lean Production und gleichermassen auf den vielschichtigen Leistungen durch sorgfältig ausgebildete Mitarbeiter, auf dem schonenden Umgang mit Ressourcen sowie auf intelligenter Automation und schlanker Prozesse entlang der gesamten Wertschöpfungskette – von der Idee bis zum fertigen Produkt mit allen dazugehörenden Services. Durch die mit dem Lean Prinzip einhergehende massive Senkung der Gesamtkosten bei intelligentem Umgang mit einer erhöhten Variantenvielfalt – z.B. der Luftkeimsammler – ist es Femron gelungen, sich erfolgreich am Markt zu positionieren und wettbewerbsfähig zu bleiben. Mithilfe von Lean Management wurden Konzepte entwickelt, mit deren Hilfe die Herstellkosten für das Kernprodukt der Firma signifikant gesenkt werden konnten. Massgeblich für den Erfolg war die Einführung eines Flussprinzips, das eine kontinuierliche Versorgung von Fertigungslinien sicherstellt, die Durchlaufzeit reduziert und die Implementierung des Kundentakts als Schrittmacher, der den Rhythmus der Produktion vorgibt. Die diversen Verschwendungsarten in der Produktion wurden abgestellt.
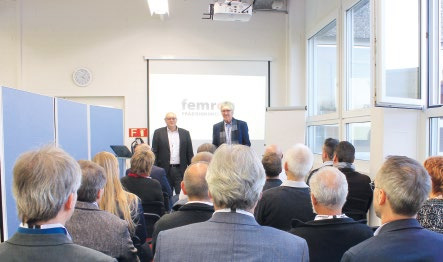
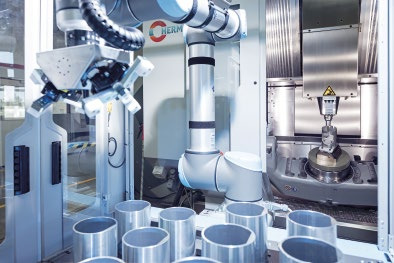
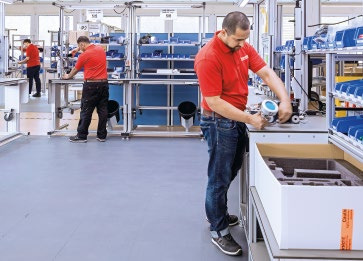
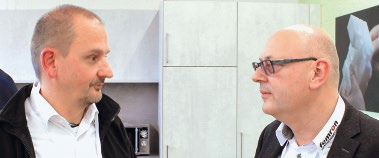
Dazu gehören u. a. die Nichtnutzung von Mitarbeiterfähigkeiten und die Nichteinforderung von Mitarbeiterleistung sowie der Abbau von hohen Beständen. Ein effizientes Lean Management wird erreicht, indem man das Pull-Prinzip anwendet, bei dem die Produktion durch eine Bestellung ausgelöst wird. Die Lagerbestände können dadurch minimiert – und die Herstellungskosten entscheidend gesenkt werden. Femron zeichnet sich vor allem dank seiner kompetenten Betreuung von Kunden, die sicher und schnell bedient werden, aus. Dank der massiven Einsparungen, die mit der Einführung des Toyotasystems einhergehen, hat es Femron geschafft, auch im aktuell schwierigen wirtschaftlichen Umfeld am Standort Schweiz zu bestehen.
Produktion der MAS-100 Luftkeimsammler
Hauptkunde ist die Firma MBV, deren Luftkeimsammler- Modelle von Anfang an bei Femron produziert wurden. Sie machen heute über 80 % des Auftragsvolumens aus. MBV ist also quasi die Schwesterfirma von Femron. MBV hat sich auch dank der hohen Qualität in der Produktion als international führender Hersteller von Luftkeimsammlern positionieren können, denn die Geräte zeichnen sich durch ihre hohe Messgenauigkeit und Zuverlässigkeit aus. Gerade die Zuverlässigkeit spielt bei den Kunden eine große Rolle. Denn fällt ein Gerät aus und lässt sich die Luftreinheit in der kontrollierten Umgebung eines Produktionsbetriebs nicht mehr mit der erforderlichen Genauigkeit kontrollieren, kann dies zu einem sofortigen Unterbruch einer Produktionslinie führen.
Die Teilnehmer konnten sich an einem Rundgang mit Präsentation ein Bild von der Fertigung und Montage bei Femron machen.
Die Teilnehmer konnten sich an einem Rundgang mit Präsentation ein Bild von der Fertigung und Montage bei Femron machen.
Präzisionsmechanik in der Fertigung
In den Fertigungsbereich ist das Konstruktions- und Programmierbüro eingebettet. Die automatische Bearbeitung an CNC Fräs- und Drehmaschinen mit Roboterunterstützung wird hier mit Hilfe von modernster CAD/CAM Software programmiert. Dies erfolgt gleichermassen für die CNC Bearbeitung von Prototypen, Einzelteilen sowie in der Serienproduktion. CAD/CAM (Computer-Aided Design und Computer-Aided Manufacturing) bezeichnet dabei Computersoftware, die beide Funktionen, Konstruktion und Bearbeitung, vereint. Die Prototypen werden am CAD entwickelt. Dabei werden Daten, die der Kunde liefert, visualisiert, d. h. Skizzen werden in Zeichnungen umgesetzt.
Bei der Kommunikation mit dem Kunden spielt die Visualisierung eine grosse Rolle. Mit Mitteln wie 3D-Laserdruck werden über Nacht Prototypen des gewünschten Werkstücks hergestellt, um gemeinsam mit dem Kunden die Umsetzung seiner Ideen Schritt für Schritt nachzuvollziehen. Alle Produktionsprozesse können am Bildschirm in 3D simuliert werden, um die Abläufe zu präzisieren. Die CAM Software verwendet Modelle aus dem CAD und generiert Werkzeugbahnen, mit deren Hilfe die physikalischen Bauteile automatisiert hergestellt werden. Die gesamte Bearbeitung wird also simuliert.
Bei der Kommunikation mit dem Kunden spielt die Visualisierung eine grosse Rolle. Mit Mitteln wie 3D-Laserdruck werden über Nacht Prototypen des gewünschten Werkstücks hergestellt, um gemeinsam mit dem Kunden die Umsetzung seiner Ideen Schritt für Schritt nachzuvollziehen. Alle Produktionsprozesse können am Bildschirm in 3D simuliert werden, um die Abläufe zu präzisieren. Die CAM Software verwendet Modelle aus dem CAD und generiert Werkzeugbahnen, mit deren Hilfe die physikalischen Bauteile automatisiert hergestellt werden. Die gesamte Bearbeitung wird also simuliert.
Mithilfe der CAM Programme können die Fräsarbeiten automatisiert von 5-achsigen CNC-Fräsmaschine übernommen werden (Abb. 2). Die Verwendung der exakt arbeitenden Maschinen ist eine Voraussetzung für die erforderliche Präzision im Optik-, Medizintechnik- und Pharmabereich.
Der beste Weg zum Erfolg!
Interview mit Herrn Norbert Schorpp, CEO der Femron AG über Lean production
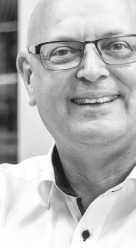
Guten Tag Herr Schorpp, Sie sind Geschäftsführer der Firma Femron. Wie ist sie entstanden?
N. Schorpp: Die Femron AG ist durch einen Management- Buy-Out im Jahr 2009 entstanden. Davor war die Firma Sinar Produzent von Fachkameras. Seit 1987 führte die Firma Sinar Lohnfertigung durch. Seit 1996 produzieren wir für die Firma MBV Luftkeimsammler.
Die Zusammenarbeit mit MBV hat demnach bereits viel früher – noch vor der Firmengründung von Femron – angefangen?
N. Schorpp: Ja, von den ersten Prototypen an haben wir die Luftkeimsammler-Modelle produziert. Seit 2009 sind wir selbständig als eigenständige Firma, wobei ich selber Miteigentümer dieser AG bin. Der Hauptkunde ist die Firma MBV mit über 80 % des Auftragsvolumens. MBV ist also unsere Schwesterfirma.
Welche Firmenphilosophie ist Ihnen wichtig?
N. Schorpp: Vor 20 Jahren haben wir die Produktion der Luftkeimsammler mit einer ganz normalen Serienfertigung begonnen. Wir haben also 50 x die Vormontage des einen Prozesses, dann die Vormontage des nächsten durchgeführt. Jeder Prozess für sich war eigentlich effizient, weil man fünfzigmal die gleiche Tätigkeit durchgeführt hat, aber man hatte kein fertiges Produkt, dafür sehr hohe Zwischenstände am Lager. Man blockierte sich gegenseitig, da schließlich mehrere verschiedene Typen von Luftkeimsammlern produziert wurden. Von dem einen Typ hatte man dann viele auf Lager, vom anderen Typ dagegen nichts, da uns der Platz für das Lager fehlte. Der Markt hingegen, der Kunde, wünscht heute fünf Modelle vom einen Typ, morgen zehn Modelle vom anderen. Wir waren ständig im Lieferverzug. Wir führten in der Folge den One-Piece-Flow ein.
In der Montage ist für uns die One-Piece-Flow-Technik sehr wichtig. Sie bringt sehr viel an Effizienz: wir haben damit die Montagezeiten aller unserer Produkte glatt halbiert. In dem neuen System muss man sich nicht mit der Beschaffung von Material und Werkzeug beschäftigen, sondern man kann sich der Montagetätigkeit, also der Wertschöpfung, widmen. In der Montage beschäftigen und benötigen wir nach der Umstellung nur sechs Mitarbeiter.
Die nicht wertschöpfenden Tätigkeiten, z. B. Freischaffungsprozesse für die Arbeitsfläche, Werkzeugsuche, etc., konnten wir weitgehend eliminieren. Natürlich erfordert das Investitionen, denn eine einfache Werkbank ist billiger als ein One-Piece-Flow-Arbeitsplatz. Diese Investition rechnete sich jedoch bereits innert eines Jahres. Ein weiterer Vorteil ergibt sich dadurch, dass wir einen sehr gut strukturierten Arbeitsablauf haben. Daher sind die Fehlerquellen sehr gering und die Einarbeitungszeit für unsere Mitarbeiter ist kürzer. Der Mitarbeiter hat immer die richtige Anleitung am Arbeitsplatz und keine falschen Werkzeuge. Die Einlernzeit für unsere Mitarbeiter an der Seite eines sogenannten „Götti“ ist deutlich kürzer als früher.
Die Atmosphäre in Ihrer Firma ist auffallend gut. Wie erreichen Sie das?
N. Schorpp: Das Betriebsklima liegt uns allen sehr am Herzen. Wir wollen ein attraktiver Arbeitgeber sein, allerdings steigern wir unsere Attraktivität nicht über das Gehalt, sondern über ein gutes Betriebsklima, gute Sozialleistungen, Wertschätzung und Firmenanlässe. Wir unternehmen relativ viel auch außerhalb unserer Firma. Wie etwa ein Nachtessen oder Eisstockschießen. Früher hatten wir mehr mit Druck zu kämpfen. Weil wir nicht so schnell liefern konnten, waren wir permanent in Lieferverzug. Der Druck durch den Kunden auf uns und schließlich von uns auf die Mitarbeiter war höher.
Jetzt läuft die Produktion schneller, besser, effizienter, und der Druck nimmt ab; die Atmosphäre ist entspannter. Wir können lockerer auch höhere Ziele erreichen. Das gleiche gilt auch für die Fabrikation. Vor sieben Jahren hatten wir noch 16 CNC Maschinen, heute haben wir 9 neue und effizientere CNC Maschinen, und dabei ist die Produktivität höher, weil wir die Betriebsmittel besser, d. h. effektiver, einsetzen.
Man kann während intensiver Phasen Mehrleistung von den Mitarbeiter einfordern, aber man benötigt auch Phasen zur Erholung. Es ist wichtig, die Mitarbeiter nicht zu überlasten das bringt auf Dauer nichts.
Wie arbeiten Sie mit MBV zusammen?
N. Schorpp: Einmal pro Woche haben wir ein Meeting mit MBV mit unseren Abteilungsleitern, das etwa eine Stunde dauert. Auch im operativen Bereich, dem Verkauf und im Backoffice, gibt es ein wöchentliches Meeting, bei dem es um Terminabsprachen geht. Denn Kommunikation ist heutzutage wichtig: wissen, was möchte der Partner, wo setzen wir die Prioritäten? Man muss aufeinander hören, die Prioritäten untereinander abstimmen. An solch einer Telefonkonferenz kann man sich dann auf eine gemeinsame Prioritätenliste einigen.
Wie sind Sie bezüglich der Kunden aufgestellt?
N. Schorpp: Wir haben ausschließlich langjährige Kunden, einige aus der Schweiz, aber auch aus Süddeutschland. Wir sind derzeit so ausgelastet, dass es für Neukunden schwieriger wird, Aufträge bei uns einzureichen. Denn wir können nicht bestehende Kunden für Neukunden vertrösten. Bestehende Kunden haben das Recht, so schnell und so gut wie möglich bedient zu werden. Wir wollen auch nicht zu schnell wachsen, unsere Kapazitäten nicht zu rasch ausbauen, denn dann kann man stolpern. Wir legen Wert auf ein gesundes Wachstum. In diesem Jahr sind wir von 20 auf 27 Mitarbeiter gewachsen, und das ist das Maximum dessen, was wir uns zutrauen sollten. Denn sonst leidet die Qualität.
Welche Erfahrungen für die Zukunft nehmen Sie als Organisator dieses SwissCCS Events mit?
N. Schorpp: Die meisten Besucher kamen aus einem ganz anderen Bereich und ich finde es immer wieder inspirierend, dass auch andere Bereiche ähnliche strukturelle Herausforderungen zu bearbeiten haben. Ob ich nun wie in der Präzisionsmechanik effizient Teile fräse, drehe und montiere oder ob ich effizient eine Pille herstelle, das Vorgehen sollte trotz unterschiedlicher Prozesse dahinter immer gleich sein. Man muss versuchen, den Lean-Gedanken mitzutragen, um eine verschwendungsfreie Fertigung hinzubekommen.
Welche Rolle spielt für Femron der Standort?
N. Schorpp: Die große Herausforderung für den Standort Mitteleuropa ist es natürlich, so viel wie möglich den Faktor Lohnkosten zu senken, denn bei allem was Lohn-intensiv und nicht wertschöpfend ist, haben wir in Mitteleuropa einen grossen Nachteil.
In Sparten wie unserer, in der es darum geht hochpräzise Produkte hoher Qualität herzustellen, und auch dort, wo wir effizient automatisieren können, spielen die Lohnkosten nicht mehr so eine große Rolle. Für diese Produktionssparten ist der Standort Schweiz natürlich ideal! Nachteile sind natürlich die Lohnkosten und der hohe Wechselkurs. Aber wenn man nur wegen dem Wechselkurs seine Strategie nicht durchziehen kann, dann war schon vorher etwas nicht in Ordnung, bzw. es ist aktuell auch etwas anderes nicht in Ordnung. Wenn man sich nicht rechtzeitig Gedanken über die Prozessoptimierung macht, ist man schnell einmal abseits vom Markt. Man muss ständig an den Prozessen arbeiten, man darf sich einfach nicht ausruhen. Das ist mühsam, aber es ist der beste Weg zum Erfolg!
Herr Schorpp, vielen Dank für Ihre Zeit und die Ausführungen. Wir wünschen Ihnen weiterhin viel Erfolg und alles Gute für die Zukunft.
N. Schorpp: Die Femron AG ist durch einen Management- Buy-Out im Jahr 2009 entstanden. Davor war die Firma Sinar Produzent von Fachkameras. Seit 1987 führte die Firma Sinar Lohnfertigung durch. Seit 1996 produzieren wir für die Firma MBV Luftkeimsammler.
Die Zusammenarbeit mit MBV hat demnach bereits viel früher – noch vor der Firmengründung von Femron – angefangen?
N. Schorpp: Ja, von den ersten Prototypen an haben wir die Luftkeimsammler-Modelle produziert. Seit 2009 sind wir selbständig als eigenständige Firma, wobei ich selber Miteigentümer dieser AG bin. Der Hauptkunde ist die Firma MBV mit über 80 % des Auftragsvolumens. MBV ist also unsere Schwesterfirma.
Welche Firmenphilosophie ist Ihnen wichtig?
N. Schorpp: Vor 20 Jahren haben wir die Produktion der Luftkeimsammler mit einer ganz normalen Serienfertigung begonnen. Wir haben also 50 x die Vormontage des einen Prozesses, dann die Vormontage des nächsten durchgeführt. Jeder Prozess für sich war eigentlich effizient, weil man fünfzigmal die gleiche Tätigkeit durchgeführt hat, aber man hatte kein fertiges Produkt, dafür sehr hohe Zwischenstände am Lager. Man blockierte sich gegenseitig, da schließlich mehrere verschiedene Typen von Luftkeimsammlern produziert wurden. Von dem einen Typ hatte man dann viele auf Lager, vom anderen Typ dagegen nichts, da uns der Platz für das Lager fehlte. Der Markt hingegen, der Kunde, wünscht heute fünf Modelle vom einen Typ, morgen zehn Modelle vom anderen. Wir waren ständig im Lieferverzug. Wir führten in der Folge den One-Piece-Flow ein.
In der Montage ist für uns die One-Piece-Flow-Technik sehr wichtig. Sie bringt sehr viel an Effizienz: wir haben damit die Montagezeiten aller unserer Produkte glatt halbiert. In dem neuen System muss man sich nicht mit der Beschaffung von Material und Werkzeug beschäftigen, sondern man kann sich der Montagetätigkeit, also der Wertschöpfung, widmen. In der Montage beschäftigen und benötigen wir nach der Umstellung nur sechs Mitarbeiter.
Die nicht wertschöpfenden Tätigkeiten, z. B. Freischaffungsprozesse für die Arbeitsfläche, Werkzeugsuche, etc., konnten wir weitgehend eliminieren. Natürlich erfordert das Investitionen, denn eine einfache Werkbank ist billiger als ein One-Piece-Flow-Arbeitsplatz. Diese Investition rechnete sich jedoch bereits innert eines Jahres. Ein weiterer Vorteil ergibt sich dadurch, dass wir einen sehr gut strukturierten Arbeitsablauf haben. Daher sind die Fehlerquellen sehr gering und die Einarbeitungszeit für unsere Mitarbeiter ist kürzer. Der Mitarbeiter hat immer die richtige Anleitung am Arbeitsplatz und keine falschen Werkzeuge. Die Einlernzeit für unsere Mitarbeiter an der Seite eines sogenannten „Götti“ ist deutlich kürzer als früher.
Die Atmosphäre in Ihrer Firma ist auffallend gut. Wie erreichen Sie das?
N. Schorpp: Das Betriebsklima liegt uns allen sehr am Herzen. Wir wollen ein attraktiver Arbeitgeber sein, allerdings steigern wir unsere Attraktivität nicht über das Gehalt, sondern über ein gutes Betriebsklima, gute Sozialleistungen, Wertschätzung und Firmenanlässe. Wir unternehmen relativ viel auch außerhalb unserer Firma. Wie etwa ein Nachtessen oder Eisstockschießen. Früher hatten wir mehr mit Druck zu kämpfen. Weil wir nicht so schnell liefern konnten, waren wir permanent in Lieferverzug. Der Druck durch den Kunden auf uns und schließlich von uns auf die Mitarbeiter war höher.
Jetzt läuft die Produktion schneller, besser, effizienter, und der Druck nimmt ab; die Atmosphäre ist entspannter. Wir können lockerer auch höhere Ziele erreichen. Das gleiche gilt auch für die Fabrikation. Vor sieben Jahren hatten wir noch 16 CNC Maschinen, heute haben wir 9 neue und effizientere CNC Maschinen, und dabei ist die Produktivität höher, weil wir die Betriebsmittel besser, d. h. effektiver, einsetzen.
Man kann während intensiver Phasen Mehrleistung von den Mitarbeiter einfordern, aber man benötigt auch Phasen zur Erholung. Es ist wichtig, die Mitarbeiter nicht zu überlasten das bringt auf Dauer nichts.
Wie arbeiten Sie mit MBV zusammen?
N. Schorpp: Einmal pro Woche haben wir ein Meeting mit MBV mit unseren Abteilungsleitern, das etwa eine Stunde dauert. Auch im operativen Bereich, dem Verkauf und im Backoffice, gibt es ein wöchentliches Meeting, bei dem es um Terminabsprachen geht. Denn Kommunikation ist heutzutage wichtig: wissen, was möchte der Partner, wo setzen wir die Prioritäten? Man muss aufeinander hören, die Prioritäten untereinander abstimmen. An solch einer Telefonkonferenz kann man sich dann auf eine gemeinsame Prioritätenliste einigen.
Wie sind Sie bezüglich der Kunden aufgestellt?
N. Schorpp: Wir haben ausschließlich langjährige Kunden, einige aus der Schweiz, aber auch aus Süddeutschland. Wir sind derzeit so ausgelastet, dass es für Neukunden schwieriger wird, Aufträge bei uns einzureichen. Denn wir können nicht bestehende Kunden für Neukunden vertrösten. Bestehende Kunden haben das Recht, so schnell und so gut wie möglich bedient zu werden. Wir wollen auch nicht zu schnell wachsen, unsere Kapazitäten nicht zu rasch ausbauen, denn dann kann man stolpern. Wir legen Wert auf ein gesundes Wachstum. In diesem Jahr sind wir von 20 auf 27 Mitarbeiter gewachsen, und das ist das Maximum dessen, was wir uns zutrauen sollten. Denn sonst leidet die Qualität.
Welche Erfahrungen für die Zukunft nehmen Sie als Organisator dieses SwissCCS Events mit?
N. Schorpp: Die meisten Besucher kamen aus einem ganz anderen Bereich und ich finde es immer wieder inspirierend, dass auch andere Bereiche ähnliche strukturelle Herausforderungen zu bearbeiten haben. Ob ich nun wie in der Präzisionsmechanik effizient Teile fräse, drehe und montiere oder ob ich effizient eine Pille herstelle, das Vorgehen sollte trotz unterschiedlicher Prozesse dahinter immer gleich sein. Man muss versuchen, den Lean-Gedanken mitzutragen, um eine verschwendungsfreie Fertigung hinzubekommen.
Welche Rolle spielt für Femron der Standort?
N. Schorpp: Die große Herausforderung für den Standort Mitteleuropa ist es natürlich, so viel wie möglich den Faktor Lohnkosten zu senken, denn bei allem was Lohn-intensiv und nicht wertschöpfend ist, haben wir in Mitteleuropa einen grossen Nachteil.
In Sparten wie unserer, in der es darum geht hochpräzise Produkte hoher Qualität herzustellen, und auch dort, wo wir effizient automatisieren können, spielen die Lohnkosten nicht mehr so eine große Rolle. Für diese Produktionssparten ist der Standort Schweiz natürlich ideal! Nachteile sind natürlich die Lohnkosten und der hohe Wechselkurs. Aber wenn man nur wegen dem Wechselkurs seine Strategie nicht durchziehen kann, dann war schon vorher etwas nicht in Ordnung, bzw. es ist aktuell auch etwas anderes nicht in Ordnung. Wenn man sich nicht rechtzeitig Gedanken über die Prozessoptimierung macht, ist man schnell einmal abseits vom Markt. Man muss ständig an den Prozessen arbeiten, man darf sich einfach nicht ausruhen. Das ist mühsam, aber es ist der beste Weg zum Erfolg!
Herr Schorpp, vielen Dank für Ihre Zeit und die Ausführungen. Wir wünschen Ihnen weiterhin viel Erfolg und alles Gute für die Zukunft.
Das Interview führte Frau v. Kieckebusch-Gück von der Redaktion ReinRaumTechnik.
Roboter fräsen im 24 Stunden-Betrieb
Die Fertigungsprozesse werden abschnittsweise organisiert, um die Anzahl der Arbeitsschritte überschaubar zu halten. Nach der Beendigung eines Fertigungsschritts erhalten die Produkte eine Zwischenverpackung zum Schutz der Teile und werden in der nächsten Fertigungseinheit weiterverarbeitet.
In der Fertigung spielt die Luftqualität eine grosse Rolle. Die Temperatur wird konstant eingeregelt, Schallelemente senken die Lautstärke auf maximal 72 db ab. Dies dient der Qualität der Produkte und dem Wohlbefinden der Mitarbeiter.
In der Fertigung spielt die Luftqualität eine grosse Rolle. Die Temperatur wird konstant eingeregelt, Schallelemente senken die Lautstärke auf maximal 72 db ab. Dies dient der Qualität der Produkte und dem Wohlbefinden der Mitarbeiter.
Qualitätsprüfung
Die Produktion bei Femron zeichnet sich durch eine detaillierte Planung und hohe Prozesssicherheit aus, was zu einer besseren Produktqualität nach internationalen Standards führt. Der erste Teil einer Produktionslinie wird immer speziell geprüft. Auch nach jedem Zyklus der Produktion gibt es eine taktile Messung zur Überprüfung der Genauigkeit. Vor der Messung wird eine automatische Reinigung durchgeführt, um zu vermeiden, dass Späne und andere Verunreinigungen die Messung verfälschen. Denn bei Femron werden vorwiegend hochpräzise Produkte mit Toleranzen im μm-Bereich gefertigt. Die Dokumentation und Archivierung dient dem Nachweis einer transparenten Prozesskette.
Der Prüfraum ist als Sauberraum spezifiziert. Eine Filteranlage arbeitet mit Überdruck, um einen exakten Messvorgang zu ermöglichen.
Der Prüfraum ist als Sauberraum spezifiziert. Eine Filteranlage arbeitet mit Überdruck, um einen exakten Messvorgang zu ermöglichen.
One-Piece-Flow Montagebereich
Der wichtigste Schritt, die Montage der Teile und der Elektronik ist eine Aufgabe, der sich aufgrund der hohen Effizienz lediglich sechs Mitarbeiter widmen (Abb. 3).
Die Teilnehmer konnten Cardboard-Modelle besichtigen, die die Entwicklung eines neuen Arbeitsplatzes unterstützen. Cardboard Engineering stellt eine Anwendung des Lean-Prinzips zur Gestaltung optimaler Arbeitsplätze und Fertigungslinien durch den Einsatz von Kartonage-Modellen des zukünftigen Arbeitsplatzes dar. Ziel ist es, die Mitarbeiter in die Entwicklung verschwendungsfreier Abläufe am Arbeitsplatz miteinzubeziehen. Alle Teile der Organisationseinheit sind sinnvoll aufgereiht und müssen in der richtigen Anordnung vorhanden sein. Die Arbeitsabläufe werden im Vorfeld aufeinander abgestimmt.
Die Teilnehmer konnten Cardboard-Modelle besichtigen, die die Entwicklung eines neuen Arbeitsplatzes unterstützen. Cardboard Engineering stellt eine Anwendung des Lean-Prinzips zur Gestaltung optimaler Arbeitsplätze und Fertigungslinien durch den Einsatz von Kartonage-Modellen des zukünftigen Arbeitsplatzes dar. Ziel ist es, die Mitarbeiter in die Entwicklung verschwendungsfreier Abläufe am Arbeitsplatz miteinzubeziehen. Alle Teile der Organisationseinheit sind sinnvoll aufgereiht und müssen in der richtigen Anordnung vorhanden sein. Die Arbeitsabläufe werden im Vorfeld aufeinander abgestimmt.
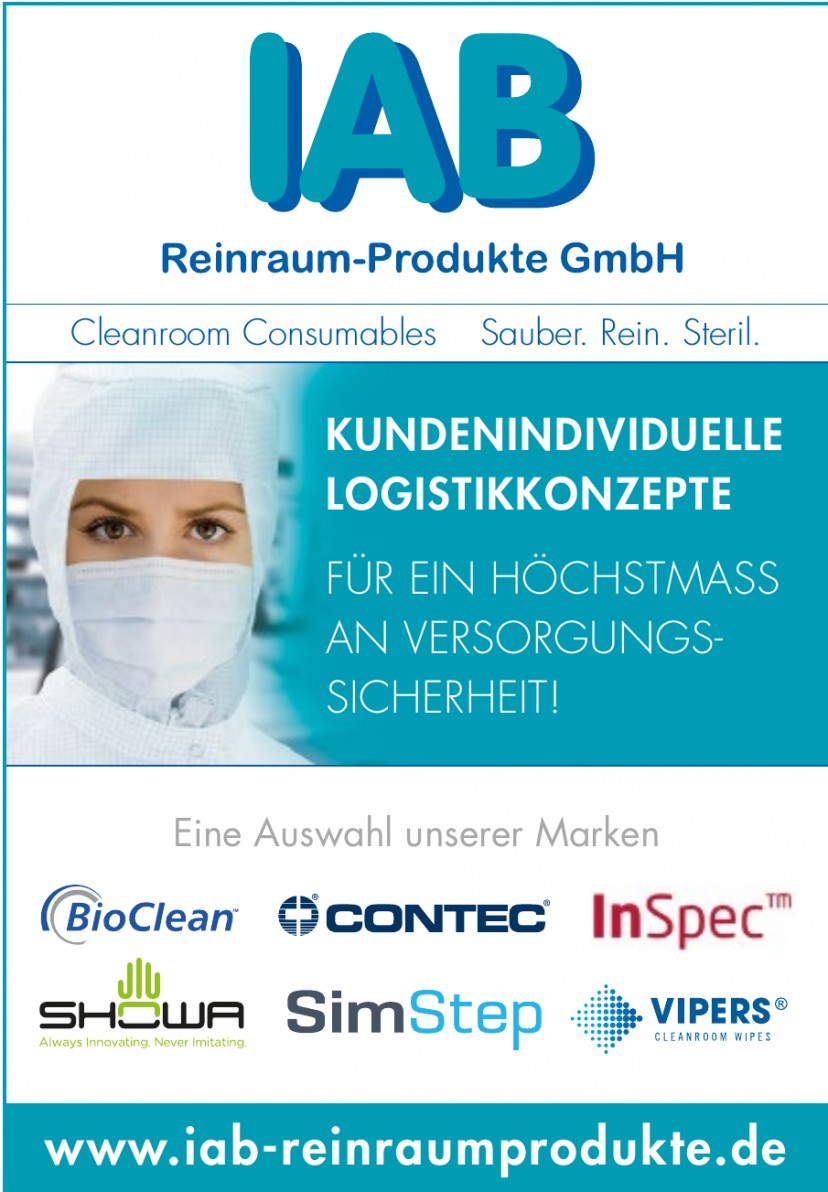
Gerade im Montage-Prozess ist die Taktung der einzelnen Schritte wichtig. Wenn die Prozesse nicht untereinander getaktet sind, blockieren sie sich gegenseitig. Der Mitarbeiter kennt die Prozesszeit und damit auch die Kosten der Montage jedes einzelnen Schrittes und kann die einzelnen Schritte optimal aufeinander abstimmen. Die zeitaufwändige automatisierte Prüfung der Elektronik eines zusammengebauten Luftkeimsammlers ist z. B. ein limitierender Faktor, der stets im Auge behalten sein will, damit er zu den anderen Montageabläufen passt.
Vom Messprotokoll bis hin zur Identifizierung einzelner Komponenten wird die Qualität der Produkte dokumentiert und und kann stets nachgewiesen werden. In diesem System ist auch die Rückverfolgbarkeit und Identifizierung defekter Komponenten gewährleistet. Eine Laser-Beschriftungsmaschine für die Etiketten versieht die wichtigen Teile eines Geräts im Sinne der Rückverfolgbarkeit mit einer Seriennummer. Zudem verfügt das Unternehmen auch über eine Lasergraviermaschine. Das Lasergravieren bewirkt, dass die Beschriftung unwiederbringlich sicher angebracht ist; sie dient daher der Sicherheit.
Bei einem abschliessenden Apéro riche versammelten sich die Gäste im Konferenzraum, um mit dem Femron-Management Fragen oder Anliegen zu diskutieren (Abb. 4). Selbstverständlich waren an diese Anlass auch die SwissCCS-Vorstände vor Ort, neben Andy und Hans Zingre begrüssten Martin Gutsche, Arnold Brunner, Werner Straub die Gäste.
Vom Messprotokoll bis hin zur Identifizierung einzelner Komponenten wird die Qualität der Produkte dokumentiert und und kann stets nachgewiesen werden. In diesem System ist auch die Rückverfolgbarkeit und Identifizierung defekter Komponenten gewährleistet. Eine Laser-Beschriftungsmaschine für die Etiketten versieht die wichtigen Teile eines Geräts im Sinne der Rückverfolgbarkeit mit einer Seriennummer. Zudem verfügt das Unternehmen auch über eine Lasergraviermaschine. Das Lasergravieren bewirkt, dass die Beschriftung unwiederbringlich sicher angebracht ist; sie dient daher der Sicherheit.
Bei einem abschliessenden Apéro riche versammelten sich die Gäste im Konferenzraum, um mit dem Femron-Management Fragen oder Anliegen zu diskutieren (Abb. 4). Selbstverständlich waren an diese Anlass auch die SwissCCS-Vorstände vor Ort, neben Andy und Hans Zingre begrüssten Martin Gutsche, Arnold Brunner, Werner Straub die Gäste.
KONTAKT
Norbert Schorpp
Femron AG, Feuerthalen, Schweiz
Tel.: +41 52 647 40 80
norbert.schorpp@femron.ch
www.femron.ch
Femron AG, Feuerthalen, Schweiz
Tel.: +41 52 647 40 80
norbert.schorpp@femron.ch
www.femron.ch