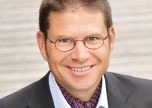
G
eschäftsführer Dietmar Pfennig berichtet: „Im Jahr 1998 hatten wir gerade mit 3 Partnerfirmen ein großes Projekt zum Abschluss gebracht: Das erste vollautomatische Verfahren zur Präparation von Moppbezügen für die Krankenhausreinigung. Für die Desinfektionskomponente war Schülke & Mayr, zu denen wir natürlich einen intensiven Kontakt pflegten, zuständig. Als während einer Jahrestagung die Industriehygienesparte mitbekommen hat, mit welch hochentwickelten Systemen wir in den Krankenhäusern tätig waren – bereits komplett berührungsfreies Arbeiten mit reproduzierbarer Benetzung – und was größtenteils der Stand der Technik in der Reinraumreinigung war – Eimer, Schwämme und Tücher – war der Entwicklungsauftrag schnell klar:Das brauchen wir in reinraumtauglich!
Natürlich mussten wir uns erst in das Thema und die Anforderungen in GMP-Bereichen hineinarbeiten, konnten die Entwicklung aber doch innerhalb eines Jahres – inklusive Zertifizierung – zum Abschluss bringen. Wir haben mit dem Reinigungswagen Clino CR3 und dem Moppbezug King CR das erste vom Fraunhofer IPA zertifizierte Reinraumreinigungssystem überhaupt auf den Markt gebracht.
Eine Sache haben wir allerdings völlig falsch eingeschätzt: Den Bedarf für ein solches Gerät. Wir sind zunächst von einigen wenigen Sonderanfertigungen ausgegangen und wurden dann von der Nachfrage regelrecht überrollt und dies in den Anfangszeiten fast nur durch Mundpropaganda begeisterter Anwender.“
Das Hauptargument war damals natürlich die erhebliche Zeiteinsparung gegenüber den herkömmlichen Verfahren, sowie das deutlich ergonomischere Arbeiten und die Möglichkeit, Equipment und Moppbezüge problemlos autoklavieren zu können.
Nach einigen Detailverbesserungen war jedoch bald klar, dass das um die Flachpresse herum konzipierte System am Ende seiner Entwicklungsmöglichkeiten angelangt war und auch im Reinraum die Zukunft im Bereich der vorpräparierten Bezüge liegt. Auch die deutliche Erweiterung der Möglichkeiten des Edelstahl-Modulbausystems erforderte ein „Hardware-Update“: Das Nachfolgemodell CR 4 kann nun mit nur einem Grundmodul fast alle Anforderungen realisieren.
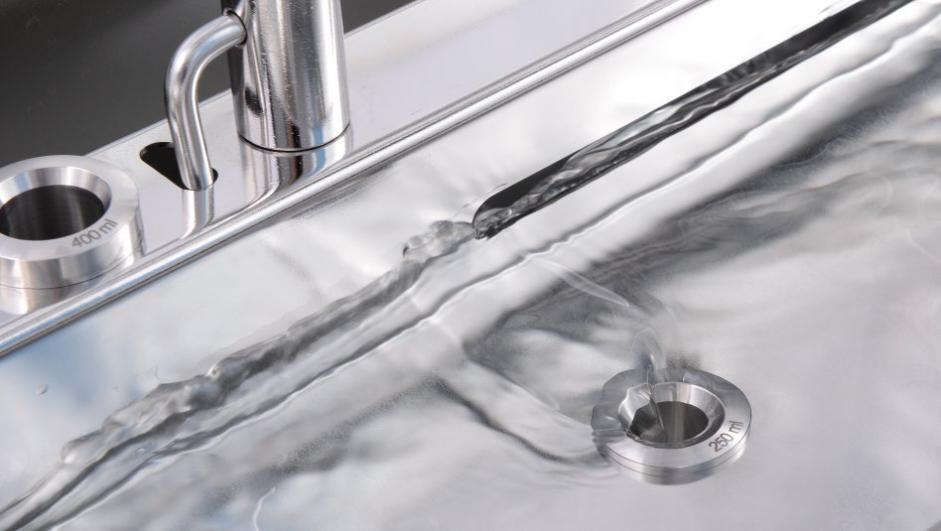

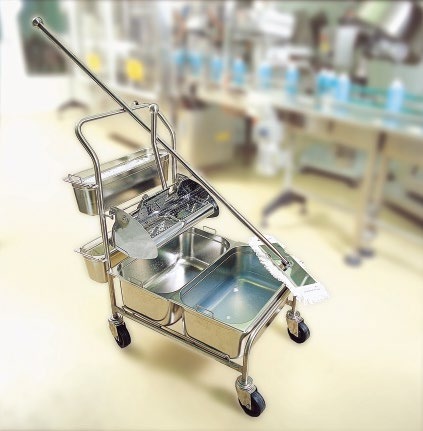
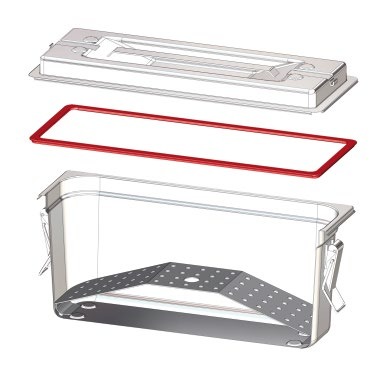
Nach zweijähriger Entwicklungszeit, verbunden mit erheblichen Investitionen in Produktionswerkzeuge, kam im Jahr 2011 mit „EasyMop GMP“ das erste benutzerunabhängig reproduzierbare Reinraumreinigungssystem auf den Markt. Die Kunden reagierten begeistert, waren doch schlagartig Probleme wie unabsichtliche Fehlbedienung, Transport offenen Wassers und Fehldosierungen gelöst. Die Verbesserungen im Prozessablauf konnten auch die Juroren auf der ContaminExpo in Paris 2015 überzeugen, so dass EasyMop GMP den Innovationspreis für Reinraumbetriebsmaterial gewinnen konnte.
Das System ist bis heute „State of the Art“ in der Reinraumreinigung, aber das heißt natürlich nicht, dass es keine weiteren Herausforderungen gegeben hätte:
Für Objekte mit schwankendem Moppbedarf sollte eine Lösung gefunden werden, jeden einzelnen Mopp unmittelbar vor seiner Benutzung zu tränken, und zwar so exakt wie möglich. Das Ergebnis einer weiteren zweijährigen Entwicklung ist das MopFloat System, das ohne Pumpen, Ventile oder ähnliches alleine durch mechanische Intelligenz eine vom Anwender nicht beeinflussbare Präzision erreicht, die in Abweichungen von weniger als 2 % resultiert.
Auch im Bereich der Textilien wurden große Fortschritte erzielt. Während es vor 20 Jahren nur einen reinraumtauglichen Moppbezug gab, existiert mittlerweile eine ganze Bandbreite von zertifizierten Textilien für den Einweg- oder Mehrwegeinsatz. Diese werden zum allergrößten Teil in der eigenen Produktion in Deutschland hergestellt und auch im Inland gewaschen und aufbereitet, um die geforderten Eigenschaften auch nachweislich garantieren zu können.
Der weit überwiegende Teil ist dabei als Mehrwegsystem konzipiert, da dies in den allermeisten Fällen die deutlich wirtschaftlichere Alternative darstellt. Um auch hier dem Anwender die erforderliche Sicherheit bieten zu können, wurde eine wissenschaftliche Langzeitstudie mit dem Textilforschungsinstitut Denkendorf initiiert (http://www.pps-pfennig.de/aufbereitung- reinheitstauglich). Das Ergebnis konnte bestätigen, dass bei bis zu 50 sterilen und bis zu 100 unsterilen Aufbereitungszyklen keine Einbußen bei Quadratmeter- und Reinigungsleistung zu befürchten sind und auch keine erhöhte Partikelabgabe stattfindet.
Betrachtet man diese Entwicklung – von der Eimer-und-Schwamm-Methode hin zum voll validierbaren und anwendersicheren Reinigungssystem – so spricht dies Bände über die gestiegene Wertigkeit und Wahrnehmung der Bedeutung einer korrekt durchgeführten Reinigung und/oder Desinfektion für den Produktionsprozess.
Oder, um es mit dem PPS-Motto zu sagen: „Sauberkeit steckt im Detail“!
Zum gemeinsamen 20-jährigen Jubiläum gratuliert die Pfennig Reinigungstechnik GmbH der ReinraumTechnik recht herzlich.
Als kleine Erinnerung an die gemeinsamen Anfänge vor 20 Jahren haben wir eine Rarität, unsere erste Veröffentlichung in der Reinraumtechnik zum Thema „Entwicklung eines Systems für die Reinigung und Desinfektion im Reinraum“, aus unserem Archiv geholt.
Wir sagen vielen Dank für die gute und langjährige Zusammenarbeit und freuen uns auf die folgenden, mindestens 20 Jahre.
Das System ist bis heute „State of the Art“ in der Reinraumreinigung, aber das heißt natürlich nicht, dass es keine weiteren Herausforderungen gegeben hätte:
Für Objekte mit schwankendem Moppbedarf sollte eine Lösung gefunden werden, jeden einzelnen Mopp unmittelbar vor seiner Benutzung zu tränken, und zwar so exakt wie möglich. Das Ergebnis einer weiteren zweijährigen Entwicklung ist das MopFloat System, das ohne Pumpen, Ventile oder ähnliches alleine durch mechanische Intelligenz eine vom Anwender nicht beeinflussbare Präzision erreicht, die in Abweichungen von weniger als 2 % resultiert.
Auch im Bereich der Textilien wurden große Fortschritte erzielt. Während es vor 20 Jahren nur einen reinraumtauglichen Moppbezug gab, existiert mittlerweile eine ganze Bandbreite von zertifizierten Textilien für den Einweg- oder Mehrwegeinsatz. Diese werden zum allergrößten Teil in der eigenen Produktion in Deutschland hergestellt und auch im Inland gewaschen und aufbereitet, um die geforderten Eigenschaften auch nachweislich garantieren zu können.
Der weit überwiegende Teil ist dabei als Mehrwegsystem konzipiert, da dies in den allermeisten Fällen die deutlich wirtschaftlichere Alternative darstellt. Um auch hier dem Anwender die erforderliche Sicherheit bieten zu können, wurde eine wissenschaftliche Langzeitstudie mit dem Textilforschungsinstitut Denkendorf initiiert (http://www.pps-pfennig.de/aufbereitung- reinheitstauglich). Das Ergebnis konnte bestätigen, dass bei bis zu 50 sterilen und bis zu 100 unsterilen Aufbereitungszyklen keine Einbußen bei Quadratmeter- und Reinigungsleistung zu befürchten sind und auch keine erhöhte Partikelabgabe stattfindet.
Betrachtet man diese Entwicklung – von der Eimer-und-Schwamm-Methode hin zum voll validierbaren und anwendersicheren Reinigungssystem – so spricht dies Bände über die gestiegene Wertigkeit und Wahrnehmung der Bedeutung einer korrekt durchgeführten Reinigung und/oder Desinfektion für den Produktionsprozess.
Oder, um es mit dem PPS-Motto zu sagen: „Sauberkeit steckt im Detail“!
Zum gemeinsamen 20-jährigen Jubiläum gratuliert die Pfennig Reinigungstechnik GmbH der ReinraumTechnik recht herzlich.
Als kleine Erinnerung an die gemeinsamen Anfänge vor 20 Jahren haben wir eine Rarität, unsere erste Veröffentlichung in der Reinraumtechnik zum Thema „Entwicklung eines Systems für die Reinigung und Desinfektion im Reinraum“, aus unserem Archiv geholt.
Wir sagen vielen Dank für die gute und langjährige Zusammenarbeit und freuen uns auf die folgenden, mindestens 20 Jahre.
AUTOR
Dietmar Pfennig,
Geschäftsführer, Pfennig Reinigungstechnik GmbH
Geschäftsführer, Pfennig Reinigungstechnik GmbH
Kontakt
Pfennig Reinigungstechnik GmbH, Durach
info@pps-pfennig.de
www.pps-pfennig.de
info@pps-pfennig.de
www.pps-pfennig.de